
What is Industry 4.0?
In order to face the challenges of the digital age, Industries from all over the world are embracing Industry 4.0.
As per Wikipedia
The Fourth Industrial Revolution is the ongoing automation of traditional manufacturing and industrial practices, using modern smart technology.
Large-scale machine-to-machine communication (M2M) and the Internet of things (IoT) are integrated for increased automation, improved communication and self-monitoring, and production of smart machines that can analyze and diagnose issues without the need for human intervention
This new Industrial Revolution is a paradigm shift that is transforming businesses across all sectors and countries, upgrading the production process from the old, linear thinking to a smarter, more effective way to work.
The term “Industrie 4.0” was first used publicly in 2011 as “Industrie 4.0” as part of an initiative to improve competitiveness in Germany’s manufacturing Industry by combining representatives from different industries (such as business, government, and academia).
The term “Industrie 4.0” was publicly introduced in the same year at the Hannover Fair.
Renowned German professor Wolfgang Wahlster is sometimes called the inventor of the “Industry 4.0” term.
Industrie 4.0 describes manufacturing management and chain production in a new way. Similarly, the fourth industrial revolution is referred to by this term.
Rise of Industry 4.0
It’s essential to understand the evolution of manufacturing in the past 150 years before going into what, whys, and how of Industry 4.0.
A world that has experienced four distinct industrial revolutions or is experiencing them at present is called the Industrial Revolution.
First Industrial Revolution:
During the late 1700s and early 1800s, the first industrial revolution occurred.
As the manufacturing industry evolved, humans began to use water and steam-powered engines, and other types of machines to perform more efficiently manual labour and assist with an improvement in labor efficiency.
Second Industrial Revolution:
In the early 20th century, steel and electricity were introduced into factories, and the world entered a second industrial revolution.
Electrical power permitted manufacturers to increase their efficiency and increased the mobility of factory equipment.
During this period, mass manufacturing ideas such as the assembly line were developed to increase productivity.
Third Industrial Revolution:
The Third Industrial Revolution, occurred in the late 20th century, after the end of the two world wars.
As manufacturers began to integrate more electronic technology into their factories by the mid-1950s, a third industrial revolution slowly emerged.
Manufacturing companies began putting more focus on automated technology and digital technology during this period, leading to a shift away from analog and mechanical technology.
The production & usage of computers (Z1 computer to supercomputer) led to extensive use of computer and communication technologies in the production process.
Fourth Industrial Revolution:
The fourth industrial revolution, Industry 4.0, has emerged within the past few decades.
Cyber-physical systems that take advantage of Internet interconnection (IoT), real-time data are integral to Industry 4.0 and thus extend the reach of digital technology from the latest decades.
Industry 4.0 proposes a more integrated, interconnected, and global production strategy.
It physically interacts with digital technology and enables improved cooperation and access across departments, partners, providers, goods, and individuals.
Industry 4.0 helps business leaders to control, analyze and use immediate information to raise efficiency, enhance procedures and drive development in every area of their operations.
Driving Forces of Industry 4.0
Generally speaking, Industry 4.0 is an approach to technology and processes with an emphasis on automation, data exchange, and other digitalization.
These are the key pillars of Industry 4.0
- Cyber-physical systems (CPS): Cyber-physical systems refer to systems where software and hardware components are seamlessly integrated towards performing well-defined tasks.
- Smart factories: In the smart factory, production facilities and logistics systems are organized without human intervention.
- Internet of things (IoT): IoT is a name for the aggregate collection of network-enabled devices, excluding traditional computers like laptops and servers.
With IoT, now, it is possible to collect, analyze, and exchange a large amount of valuable data.
- The industrial internet of things (IIoT): The industrial internet of things (IIoT) is the use of smart sensors and actuators to enhance manufacturing and industrial processes.
- Cloud computing: Cloud computing is the delivery of computing service (or computing power), over the Internet. Computing services includes, servers, storage devices, database, networking, software, analytics & much more….
To fully implement intelligent manufacturing, engineering, supply chain integration, production, sales, and service integration are all required.
This is made possible by cloud computing.
In addition, the cloud allows for more cost-effective and efficient processing of large amounts of data that are typically stored and analysed.
Small and medium-sized businesses can also reduce their start-up costs by leveraging cloud computing, which can help them tailor their needs as their businesses grow.
- Smart manufacturing: It is technology-driven approach that encompasses fully integrated, collaborative manufacturing systems that employ internet-integrated machinery to monitor manufacturing processes in real-time.
- Cognitive computing: Cognitive computing includes technology platforms that combine machine learning, reasoning, natural language processing, speech, vision, and human computer intervention that mimic the human brain, and solve problems without human assistance
- Artificial intelligence & Machine Learning: In addition to leveraging information generated by the factory floor, manufacturing organizations can use AI and machine learning tools to take full advantage of information generated across their business units and even from partners and third parties.
Through machine learning and artificial intelligence, operations and business processes can be predicted and automated, providing visibility and predictability.
Machines used for manufacturing are prone to breakdowns during production. Machine learning algorithms may be applied to the data collected from these assets to provide businesses with more uptime and more efficiency.
Benefits of Industry 4.0:
Product life cycles and supply chains are covered by Industry 4.0, including design, sales, inventory, engineering, etc.
A better understanding of the production and business processes is shared at every level, which enables much more comprehensive and timely analytics.
This is a fast, in-depth summary of some of the advantages of adopting a 4.0 model for your company:
- The younger workforce finds you more appealing because of this. Investing in innovative Industry 4.0 technologies makes businesses more competitive and more likely to retain and attract new employees.
- The ability to communicate directly with clients means a better understanding of customer needs.
- Having the prototypes tested effectively and optimizing the assembly lines will reduce defects and shrinkage in factories.
- Product design and marketing time are reduced in the production of new products.
Things to watch out for
- Cyber Security:
Cybersecurity or cyber-physical systems is now an important topic for all companies.
In addition to the efficiency of manufacturing processes made possible by operational equipment (OT), this connectivity also exposes new access points for malicious attacks. Cybersecurity approaches that encompass IT and OT equipment are essential to consider when undergoing a digital transformation to Industry 4.0.
- Skilled Taskforce: To compete & succeed in Industry 4.0. we will need a team, which is trained on new technologies. This may mean, unlearning old things & learning new skills.
The pillars of technological advancement must be actively embraced by producers and system suppliers for the transformation to be actively shaped.
To address the need, we need to focus & create a good ecosystem ..which invests the required money & effort in the infrastructure and education.
The Way Ahead:
The adoption rate and manner of Industry 4.0 will differ between industries and countries.
Automotive and food-and-beverage industries, for example, have a high degree of product variants, which can take advantage of a greater degree of flexibility.
And semiconductors and pharmaceuticals, which demand high quality, will benefit from data-analytics improvements that reduce error rates.
Conclusion
Industry 4.0 is a system of smart factories that integrate computer systems and robots to make the Industry more efficient.
It’s the next phase in Industrial advancement that focuses heavily on interconnectivity, automation, machine learning, and real-time data.
The significant change in the system of Industry 4.0 is that it integrates several things that were not integrated into the old system.
In Industry 4.0, smart factories operate with a system that gives greater control over production, overall workflow and takes the help of smart monitoring and communicating technology.
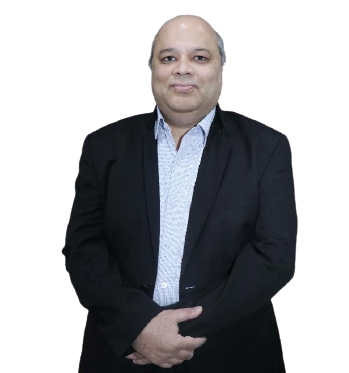