
Digital Factory: Introduction
A Digital Factory is a manufacturing facility in which people, machines, raw materials, and products are connected to each other & share real-time data (about all stages of the production process) with each other & corrective actions are taken, almost in a near real-time basis.
It is an environment in which physical things are made to interact with the digital world.
It uses digital technology for modeling, communications, and operating the manufacturing process.
As all the players (people, machine, raw material, inventory…) are connected with each other, it helps in collecting relevant data, which in turn helps in making better decisions.
Armed with real-time data, factory managers can take better decisions to configure, design, assess & evaluate various processes & with a continuous feedback loop, focus on continuous improvements.
In the digital factory, the IoT is used to allow machines to work in sync with one another, and when combined with virtual reality and human imagination, it can be used to create a tangible future for manufacturing businesses.
According to a recent Forrester report, over 90% of industrial decision-makers feel that digital transformation is crucial for the success of their firm, just 12% claim they have provided digital transition programs throughout their business.
As manufacturers look to keep up with competitors making similar advancements to theirs, integrating legacy systems is a challenge that can be a pain point.
Digital factories are now making it easier for manufacturers to scale in today’s disruptive landscape.
Find out how digital factories transform the whole manufacturing process by its successful implementation.
What is a Digital Factory?
In a digital factory, information from equipment, staff, and machinery is shared automatically throughout the process using technology.
With near-real-time data (Operational data, inventory data, data related to the shop floor, the overall process including input & output, work-in Progress…), one can improve the control of manufacturing workflows, remove bottlenecks & redundant/inefficient processes.
These are the key components of Digital Factory
- Cloud storage
- Big Data analytics
- AR & VR
- Digital Twins
- Robotics
- Industrial Internet of Things & Smart sensor
Digital production depends on an interconnected system made up of computation technologies, machinery, tools, and equipment.
Analog factories cannot be converted into digital factories by a single technology. In addition to the common technology and characteristics, digital factories have many other features as well, and the most likely manufacturers to be considered “digital factories” are those that blend multiple technologies.
Digital factories require one to undertake a complete digital journey (and this is not just a one-time investment).
For a successful digital factory, it’s important that all processes/aspects across the business are digitized.
This means, assessing, reviewing & transforming
- Sales group: Sales teams should have insight into production data, current production capabilities, etc. This will help them in taking better decisions while discussing with prospects & customers.
- Production group: They should be able to get a full view of the production process, along with robotic processes to ensure efficacy.
- Also, the quality control group, along with the production team, should be able to exercise quality control and quality testing.
(by reviewing the real-time data & doing deeper & quicker analyses).
- All teams (warehouses, shop floor, field services, sales team, procurement team, purchase department …) should have access to updated and in-depth insights into inventory, items in transit, and more.
A digital factory focuses on the following:
- A more efficient and effective & standardized planning process
- On-time-Delivery of the finished products
- Better control on various cost items such as Capex & Inventory, logistic, labour cost, transportation. Enhanced adoption of highly modern supply chain systems brings down operational costs and streamlines production.
- Go-to-market time is shorter
- Transparency in communication
- Small manufacturers are able to customize products, giving them a chance to compete with larger organizations.
- Managing knowledge effectively
- Increase in overall productivity
- Heightened forecasting capabilities and inventory optimization utilize existing capabilities for current market requirements.
- An automated & controlled process also helps in the creation of a safe environment (safety for shop floor workers, reduction in environment hazardous output..)
Why Establish Digital Factories?
Through continuous feedback in digital factories, manufacturing processes can be continuously optimized, enabling greater innovation and increases in production efficiency.
With a more collaborative process of thinking, easier and faster product development, and faster production, the entire production process optimizes while catering to customer needs.
By maximizing the power of the digital, organizations can gradually introduce new processes and instill a new digital culture in a phased fashion.
Introducing smart factories into the global economy would add $500 billion to $1.5 trillion to the global economy, according to the Capgemini report.
Also, the usage of various technologies like digital twins and co-bots are helping businesses become more agile and efficient.
Moreover, digital factories are predicted to boost efficiency by about 12% over the next five years, according to one analyst report.
A digital factory will lay the foundation for an innovative, creative work environment in an organization if it is successfully implemented and allows for collaboration and co-creation.
It means that production is much faster than it currently is. Products can be available within weeks. As a result, it is drastically reducing the product’s time to market.
Ways to Ensure Success of a Digital Factory:
Here are a few principles that will ensure success for the digital factory
- Clear vision and mission.
- Smooth collaboration between different functions.
- Smart and thoughtful leadership.
- Aligning business needs with the development process.
- A proactive team.
Challenges in the establishment of Digital Factories:
With Industry 4.0, digital factories have played a key role in revolutionizing the manufacturing sector.
In the process of digitizing their processes, manufacturing businesses may face several challenges. Some of the important challenges are listed below
- Data source reconciliation:
With Industry 4.0 and the Industrial Internet of Things (IIoT), a lot of data is getting generated (related to the overall manufacturing process). But the power of this data isn’t really harnessed to make improvements.
A key challenge for manufacturers setting up a digital factory is the wide variety of data sources. Converging IT, siloed groups and operational technology also poses challenges for organizations.
It can also be challenging to discover the right strategy solution platform that balances fast response time, flexibility, and scalability.
To find a solution that is most effective for the business, it must seek innovations that address each of these issues.
- Talent Acquisition:
Talent is the key to successfully implementing digital factories. Businesses often find it difficult to find the right candidate because the talent of the expert must be domain-specific.
We can address this by identifying different demographics and talent pools and creating talent initiatives.
To hire the right talent early, businesses must cooperate with the right educational institutions.
- Right Strategies Implementation.
Platforms that cover all possible risks can facilitate the creation and implementation of digital factories.
Manufacturing strategies of the future will be digital factories. They can add a dynamic touch to the products and the people of your organization, regardless of where you are in the world.
- Innovation: For digital factories to be successful and perform better, innovation is essential.
This means, reviewing the existing process, un-learning/dropping current practices wherever applicable & adopting new processes.
It can be difficult to choose the right innovative catalyst, as there are so many options currently available.
Here, by leveraging the right innovative technologies, businesses can leverage real-time digital performance management.
Final Words: Digital Factory
A digital factory uses digital technology to connect, collect & correct the overall manufacturing process.
Factory floors have already been transformed by digital manufacturing. Ten years from now, these factory floors may hardly be recognized because of rapid technological advancements.
Manufacturing operations are continuing to be transformed by the digitization of every step of the process to optimize every element along the supply chain.
The holistic and real-time data generated by digital factories increases efficiency, productivity, safety and environmental compliance.
You may also Like
What is Digital Manufacturing and What are the Advantages of using it?
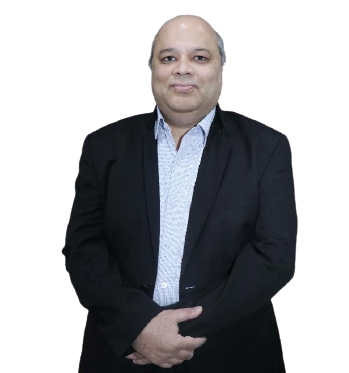